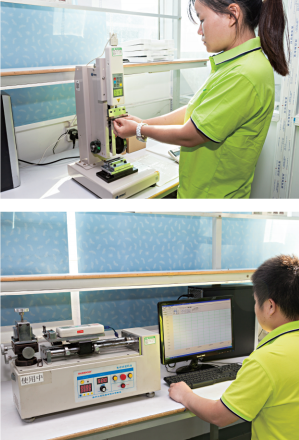
After preliminary analysis, the possible factors causing the failure include virtual welding at the welding part of the connector and the printed board, and the presence of contaminants in the connector ring hole. After inspecting the faulty connector b, it was found that no contaminants were seen in the socket of the connector. After cleaning the ring, the failure phenomenon remained the same. On the basis of the above-mentioned soil work, the welding quality of the surface mount connector is inspected. The inspection methods that can be taken include X-ray inspection and optical inspection without destroying the faulty parts.
1. Optical inspection
Use optical instruments to inspect the visible solder joints of the connector, and the inspection results are shown in Figure 3 and Figure 4. It can be seen from Fig. 3 that there is an obvious contour separation line between the solder and the auxiliary base body of the solder, and it can be seen from Fig. 4 that the size of the solder at the pad end of the printed board becomes smaller.
2. X-ray inspection
Since the wire-to-wire connector cannot be inspected by an ordinary optical microscope after welding, the welding quality of all the solder joints can not be inspected. Therefore, the X-ray inspection equipment commonly used in the industry is used to inspect the connectors on each pair of modules. The test results show that the connector is 180 The solder joints have the same shape, and the solder joints are not very good. At the same time, it can be seen from the image towel that the solder pitch of the solder joints of the connector is not equal, that is, the offset has occurred.